Waterjet Chillers: Two Styles
Hensley Thermodynamics is the maker of 2 styles of waterjet chillers:
- Recirculating Chillers
- Flow Through Chillers
We affectionately call our chillers “HT Chillers” for Hensley Thermodynamics Chillers.
Specifically Designed for the Waterjet Industry
✅ Protect your pump seals
✅ Prolong the life of your pump
✅ 10-15% higher cutting speeds
HT Chillers are designed specifically for waterjet cutting machines to reduce waterjet machine downtime due to heat related pump seal failure. Decrease your waterjet pump maintenance frequency by adding one of the most important waterjet assessories… a waterjet chiller.
To extend the life of your waterjet pump and to protect your pump manufacturer warranty, it is critical to keep the pump water temperature between 45°F and 65°F. Water temperatures above the recommended values cause the pump seals to wear and fail sooner.
Extend the life of your equipment by cooling the water with a chiller.
Keep your Recirculating Coolant or Flow-Through Water Cold
The internal Chiller Barrel Energy Storage Tank holds approximately 55 gallons of water used to store refrigeration energy. The storage tank has a capacity of “storing” 11,000 BTUs of energy and the HT Chiller produces a nominal 36,000 BTUs. The HT Chiller can efficiently handle constant cutting even when the incoming water/coolant is above 90°F.
Refrigerant lines submerged in the Chiller Barrel Energy Storage Tank first remove heat from water/coolant traveling through the lines going to the waterjet. Then, any unused refrigeration capacity not used by the water/coolant lines is stored in the Chiller Barrel Energy Storage Tank. This ability to store energy saves energy because the HT Chiller is not running needlessly when you are working in light load conditions, changing material, and re-setting up.
When the water in the Chiller Barrel reaches 45°F, the condensing unit cycles off to save energy. The cold water in the Chiller Barrel continues to absorb heat in the water/coolant lines going to the waterjet. When the line out temperature reaches approximately 58°F, the condenser unit cycles on to once again lower the Chiller Barrel water temperature to 45°F.
Our Recirculating Chillers
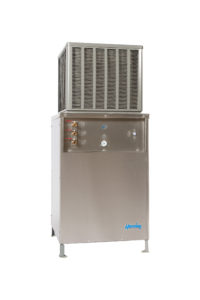
The HT Recirculating Chiller provides chilled recirculating coolant to equipment that requires coolant below 65°F with a flow rate of up to 11 gallons per minute at 50 psi.
Now you can use water instead of glycol. Water is more efficient than glycol so we designed our chillers to use water. While glycol can still be used, you’ll be more efficient with water.
Now you can stop dumping cooling water down the drain. Recirculate your waterjet cooling water. If you’re using 3, 5, 11 gallons of cooling water per minute over an 8 hour day, or running continuously cutting 24-hours a day… that’s a lot of water dumping down the drain.
✅ Reduce your water bill
✅ Reduce your sewer bill
✅ Help the environment
Our Flow Through Chillers
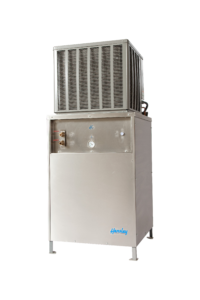
The HT Flow Through Waterjet Chiller is a flow-through system that efficiently provides chilled water to a waterjet cutting machine.
Our HT Flow Through Chiller is designed specifically for the water usage requirements of a waterjet machine (1 to 8 gallons/minute) and is a true waterjet chiller that can handle 95°F incoming water temperatures; dropping the temperature of the water going to the waterjet to below 65°F without having to oversize its capacity.
✅ True Waterjet Chiller
✅ Can handle 95°F incoming water
If you’re in the market for either a chiller for direct drive pump or a chiller for intensifier pump, you’re in the right place. Our waterjet pump chillers extend the life of your pump and reduce your waterjet pump maintenance frequency by reducing the temperature that your waterjet pump seal is exposed to. Our HT Waterjet Chiller technology is specially designed for waterjet cutters because we are waterjet owners ourselves and decided to design the best waterjet chiller solution.